measuring arrow straightness
measuring arrow straightness
Does anyone know how the arrow manufactures measure arrow straightness? I just got some Easton powerbolts and I want to measure them and post the results. To be fair it should be done like they do it.
If it breaks replace it with a bigger piece of steel
-
- Posts: 5701
- Joined: Fri Aug 04, 2006 8:36 pm
- Location: Decatur County, Indiana
-
- Posts: 6148
- Joined: Thu Nov 30, 2006 4:56 pm
- Location: Woodstock, Brantford'ish, ON
- Contact:
Easiest way is to look through it with no nock or insert, the circular image you see will show any imperfections.
The other way I have is to use a Mitutoyo dial indicator gauge on a rig that was shown to me for checking for arrow head wobble, I modified that idea to ride along the shaft of the arrow and look for imperfections as it spins.
Although it is a fun process, I have not found one that wasn't true yet.
Welcome to the forum!
The other way I have is to use a Mitutoyo dial indicator gauge on a rig that was shown to me for checking for arrow head wobble, I modified that idea to ride along the shaft of the arrow and look for imperfections as it spins.
Although it is a fun process, I have not found one that wasn't true yet.
Welcome to the forum!
If you are not willing to learn, nobody can help you, if you are willing, nobody can stop you.
A bowhunter with a passion for shooting firearms.
WMU 91
Boo string
A bowhunter with a passion for shooting firearms.
WMU 91
Boo string
I know you never hear anything technical from me so this may come as a shock.
Arrow straightness can be measured using a dial indicator taking several measurements along the length of the shaft while the shaft is secured in test blocks and spun. This reading is referred to TIR or Total Indicated Runout.
I am sure shaft manufacturers have a tolerance set up for this measurement incorporated into their manufacturing protocols.
Now if you will forgive me, I must return to installing my groundpounder mount that I have yet to figure out.
Arrow straightness can be measured using a dial indicator taking several measurements along the length of the shaft while the shaft is secured in test blocks and spun. This reading is referred to TIR or Total Indicated Runout.
I am sure shaft manufacturers have a tolerance set up for this measurement incorporated into their manufacturing protocols.
Now if you will forgive me, I must return to installing my groundpounder mount that I have yet to figure out.

Welcome to the forum! Looks like you're another 'tweaker', you'll fit right in, lol.
here's a pic of an arrow straightener that was gifted to me due to a faulty dial indicator that I got lucky and fixed via a ball point pen spring. Since I don't shoot alums, I converted it by moving the indicator mount to one end to check wobble on bheads.
It's not totally suitable for your intents because to get what info you are looking for [total run out] you would need to spin them between centers. [ala Mike P]
So, if you have a dial indicator, you can do this by getting some threaded stock or cutting bolts down, make a lathe out of your elec pistol drill by putting it upside down in a vise and turn [file] the ends to about 60 degree points.
Then, make a frame up w/ 1x4's and drill and tap the wood uprights so you can screw the 'centers' in and adj to either hit the holes in nocks and inserts or if big enough, the centers of bare shafts.
There's a rough game plan, but gotta tell ya, doubt it's worth the effort.
At one time, somehow I came to believe true or not, GT L II's had the tightest tolerances for weight and straightness and I've been happy w/ them.
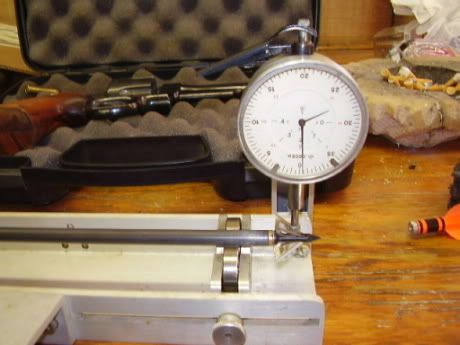
here's a pic of an arrow straightener that was gifted to me due to a faulty dial indicator that I got lucky and fixed via a ball point pen spring. Since I don't shoot alums, I converted it by moving the indicator mount to one end to check wobble on bheads.
It's not totally suitable for your intents because to get what info you are looking for [total run out] you would need to spin them between centers. [ala Mike P]
So, if you have a dial indicator, you can do this by getting some threaded stock or cutting bolts down, make a lathe out of your elec pistol drill by putting it upside down in a vise and turn [file] the ends to about 60 degree points.
Then, make a frame up w/ 1x4's and drill and tap the wood uprights so you can screw the 'centers' in and adj to either hit the holes in nocks and inserts or if big enough, the centers of bare shafts.
There's a rough game plan, but gotta tell ya, doubt it's worth the effort.
At one time, somehow I came to believe true or not, GT L II's had the tightest tolerances for weight and straightness and I've been happy w/ them.
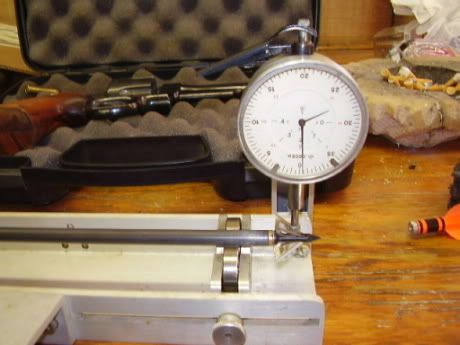
"Eze 18:21"
I give up
TIR is the deviation from the center times 2. Concentricity would be times 1. I would guess market forces being what they are the manufactures are using concentricity because it sounds better but I really don’t know. Also missing is over what distance they are measuring Easton doesn’t answer my inquires. I give up.
If it breaks replace it with a bigger piece of steel
If memory serves me right it is measured over one foot and that the amount stated refers to the single deviation from the center line.
Edit:I think it is 14", hmmmmm, welcome to the last half of my life, I am not 100% sure because 28" sounds right too!
Edit:I think it is 14", hmmmmm, welcome to the last half of my life, I am not 100% sure because 28" sounds right too!
Last edited by Boo on Fri May 22, 2009 6:35 pm, edited 1 time in total.
Some people just like stepping on rakes